Методы контроля качества: обзор эффективных инструментов на производстве
В любой уважающей себя компании контроль качества не стоит на последнем месте. Представьте: за год завод выпускает почти тысячу тонн деталей. Одна-единственная ошибка — и утром главному инженеру придется краснеть не только перед заказчиком, но и объяснять сотрудникам, куда делись месяцы труда. Брак возвращается на ремонт, порой качает весь баланс предприятия. Проглядели дефект — поставили под угрозу репутацию не только продукции, но и бренда. Все ли так серьезно? Даже хуже. Интересный факт: в 2023 году, согласно отчету Ассоциации производителей оборудования, почти 18% производственных потерь была связана с неправильным контролем качества. Причем, многие из этих ошибок обнаружили уже после отправки продукции клиенту.
Как работает система контроля качества: принципы и этапы
Не стоит думать, что весь контроль ограничивается беглым взглядом оператора на партию деталей. Современным стандартом становится многоуровневая система проверки. Раньше на заводах вполне обходились специалистами ОТК, но теперь этого мало. Для начала, разберем, как сегодня выглядит обычный цикл контроля качества на машиностроительном предприятии.
Первый этап — входящий контроль материалов. С ним все просто: доставили прутки или листы, проверили химический состав сплава, плотность, отклонения по размеру. Каждый поставщик получает свой персональный «паспорт доверия», который может со временем испортиться, если пойти на лазейку с сырьем.
Дальше — технологический контроль. Тут момент важный: на каждом этапе обработки детали — сверлении, фрезеровке, шлифовке — специалисты или автоматизированные системы оценивают критичные параметры. Часто используют специальные калибры, шаблоны, датчики, иногда даже видеокамеры и цифровые измерители с выводом данных сразу на сервер. Такой подход минимизирует шанс, что «косяк» проскочит незамеченным в следующую операцию. Согласно данным журнала Quality Progress, при автоматизации промежуточных проверок производственный брак сокращается почти на 30%.
Когда деталь готова, ее снова ждёт финальная проверка. Это уже дело не только зрения оператора, но и инструментов с точностью до сотых долей миллиметра. Здесь в ход идут все: штангенциркули, координатно-измерительные машины, ультразвуковые дефектоскопы, даже рентген-просветители. Во многих предприятиях эту процедуру проводит специальная служба, не подчинённая начальнику цеха — чтобы никто не скрыл недочёты. Известен пример: на одном оборонном заводе в 2022 году выявили факты, когда операторы снимали рентгенограммы по ночам с «идеальных» деталей и подкладывали их к бракованным. После ужесточения контроля системой двойной проверки такие манипуляции исчезли.
И последний важный этап — контроль уже после сборки или на выходе готового изделия. Иногда производят так называемые ресурсоиспытания — буквально ломают до предела по всем регламентам, чтобы убедиться: при жестких условиях ничего не полетит. На автозаводах тоже прогоняют машины на вибростендах, проверяют люфты и даже качество сварных швов ультразвуком. Конечно, 100% продукции такой контроль не проходит — только партии или выборочные экземпляры. Но этого достаточно, чтобы вовремя выявить серию с заведомыми ошибками.
Современный контроль — это, прежде всего, система управления доверием. Автоматизация, независимость контролёров, честная аналитика — вот секреты, которые позволяют обнаружить узкие места в производстве и вовремя их устранить. Если компания экономит на проверках сегодня — завтра она рискует потерять клиентов и деньги. Никто не хочет прославиться вирусным видео с отвалившимся компонентом нового автомобиля.
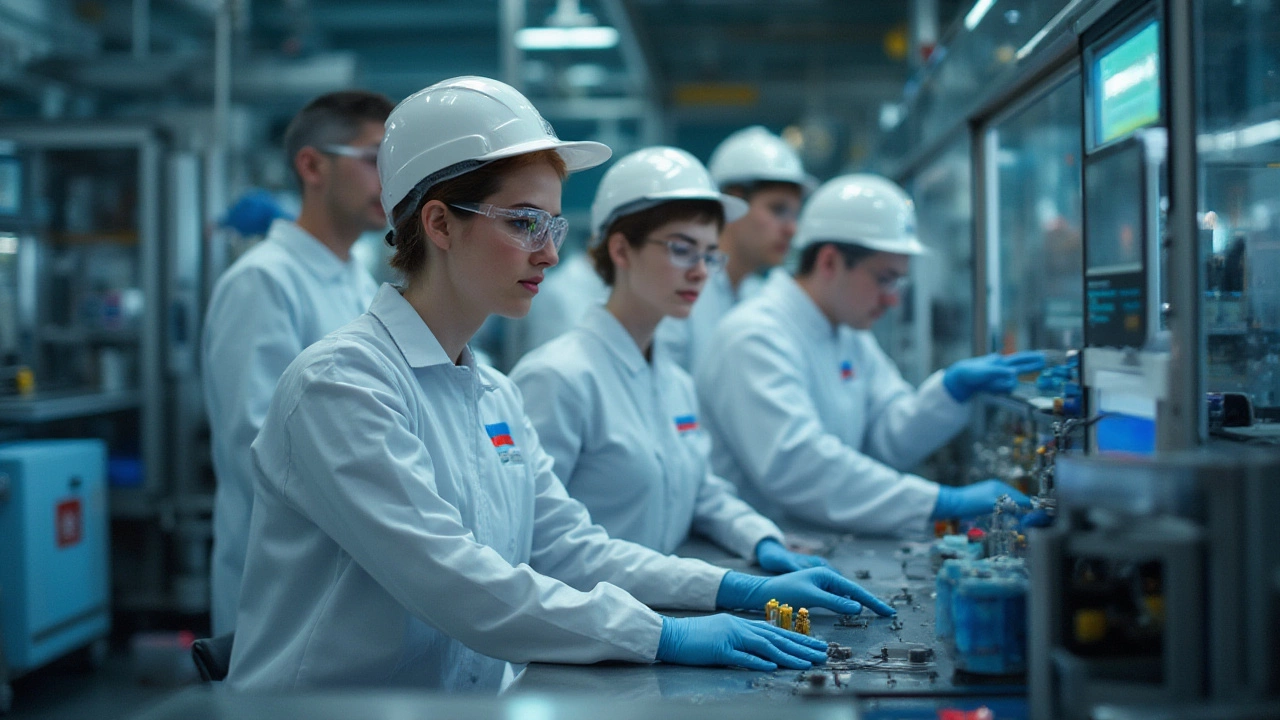
Самые популярные методы контроля качества: плюсы, минусы и любопытные детали
Заводы используют десятки инструментов контроля. Правильный метод зависит от задачи, типа продукции, объема партии, сроков и бюджета самого предприятия. Рассмотрим основные подходы, которые показывают максимальную отдачу в промышленности.
Визуальный контроль — дедовский способ, когда специалист вручную осматривает детали. Это хорошо для выявления явных дефектов: трещин, сколов, ржавчины, неправильной геометрии, скручиваний. Из плюсов — скорость и минимум затрат. Из минусов — человеческий фактор, усталость и субъективность оценок. В Японии до сих пор во многих фирмах действует принцип «глаз мастера», правда, совмещенный с цифровой фотофиксацией для последующего анализа.
Контроль с помощью измерительных инструментов — включаем здесь линейки, микрометры, поверочные плиты, специальные шаблоны, измерительные комплексы. Такой способ дает точные значения, минимизирует ошибки. Совет: если изделие серийное, заранее создайте шаблоны-калибры для проверки основных размеров. Стоимость изготовления калибра окупается за неделю, если речь идёт о массовом производстве.
Разрушающий контроль — так называют методы, при которых изделие подвергают нагрузке вплоть до разрушения. Это краш-тесты, воздействие температур, коррозии, нагрузок, проверка на излом или сжатие. Используется для опытных образцов или критически важных элементов, где отказы не допускаются. Единственный минус — «потерянная» продукция, так как образец после проверки идёт в утиль. Однажды компания Boeing заявила, что теряет почти $12 млн в год только на разрушающих ресурсных испытаниях конструкций самолётов, но эти траты окупаются многократным снижением аварий.
Неразрушающий контроль — методов много: ультразвук, магнитные поля для поиска микротрещин, рентген, вихретоковый анализ и визуализация скрытых дефектов. Здесь популярны современные системы, которые выводят картинку на дисплей и автоматически определяют участки, где параметры выходят за норму. На некоторых нефтяных и газовых предприятиях используются даже портативные дефектоскопы для экстренной проверки — прямо в полевых условиях. Современный ультразвуковой прибор сегодня помещается в карман, что было немыслимо пятнадцать лет назад.
Статистические методы — сюда входят построения карт контроля, анализ производственных трендов, поиск отклонений, автоматизация отчетности для отдела качества. Используется штучный или сплошной метод проверки — зависит от объёма выпуска. Совет от инженеров: если вы видите повторяемые мелкие дефекты из партии в партию, не ленитесь строить статистику по каждому случаю. Это позволит выявить слабое место не только в людях, но и во внезапно сбившемся оборудовании.
Современный шаг — внедрение цифровых двойников. По сути, создаётся цифровая модель детали и ее поведения, и в ней проводят десятки виртуальных «разрушений» и тестов до того, как изделие появится в цеху. Такой подход активно используют в автопроме и машиностроении. В Volvo, по публичным данным, на каждую новую серию деталей делают до 20-ти виртуальных тестов на качество, прежде чем запускать реальное производство.
Некоторые предприятия испытывают гибридные методы: ставят камеры наблюдения в цеха, чтобы следить не только за продукцией, но и за тем, как сотрудники используют инструменты. Если мастер стал чаще делать замеры наугад, а не по схеме — искусственный интеллект выдаст уведомление начальнику смены.
Пожалуй, интересный кейс: на одном китайском заводе по выпуску техники камеры с распознаванием мелких дефектов (по типу полос, царапин, сколов) полностью заменили четыре штатные смены ОТК. В итоге количество недовольных клиентов снизилось вдвое, а производительность выросла на 38%.
Каждый метод хорош в своей нише. Где-то достаточно взгляда мастера, а для микроэлектроники не обойтись без точного анализа и цифровых систем контроля. Главное — искать баланс между точностью, скоростью и человеческим фактором.
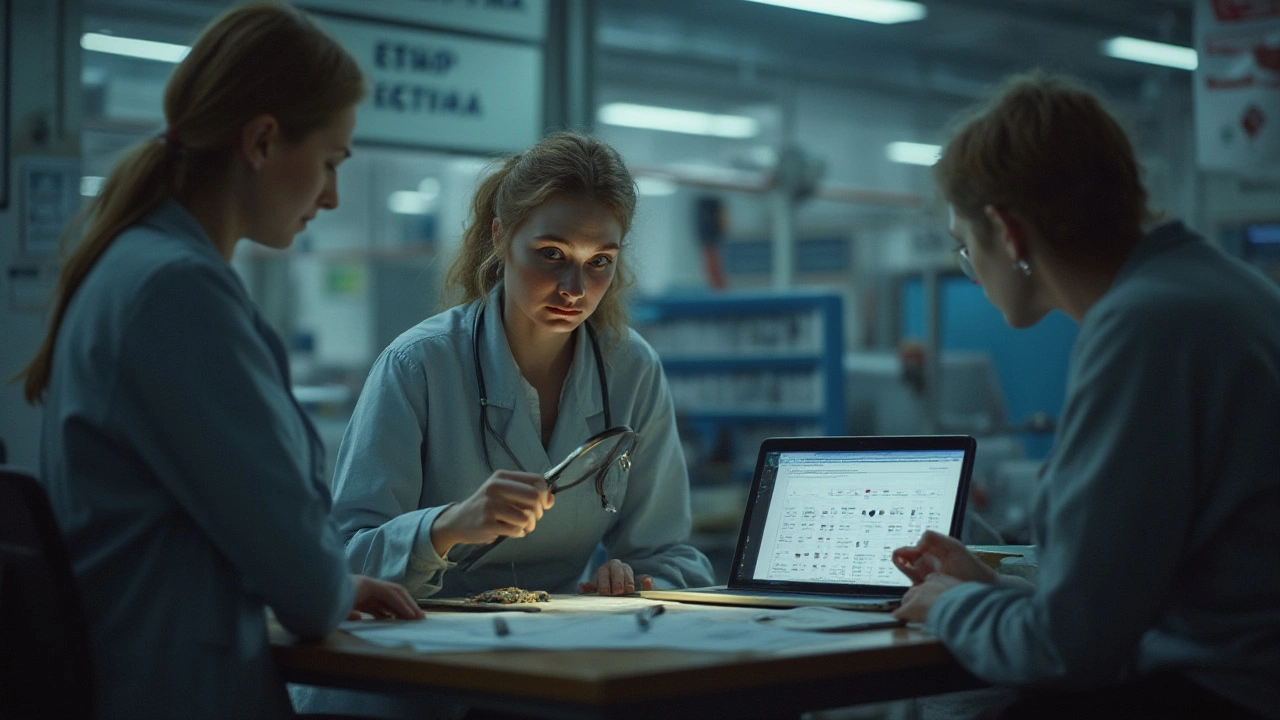
Как выбрать и внедрить эффективный метод контроля качества: практические советы
Можно годами спорить, какой способ контроля лучше — оснастка, датчики, электронные системы или рука мастера. На деле все упирается в задачу. Если вы запускаете мелкосерийное производство — излишняя автоматизация заметно съест бюджет. А вот в массовом выпуске даже простая ошибка способна стоить миллионы.
Составьте карту контролируемых точек. Для каждой точки определите уровень риска: какие дефекты там вероятнее всего, как они сказываются на конечном продукте. Такой риск-анализ позволяет избавиться от ненужных проверок и сконцентрировать силы там, где не допускается брак ни при каких условиях.
Если производство гибкое, не пожалейте времени на пилотирование новых технологий. Протестируйте цифровые датчики, видеоаналитику и автоматизированные станции. Мало кто знает, что завод Hyundai на старте 2020 года инвестировал в умные станции видеоконтроля, и за первые шесть месяцев процент возврата по браку упал с 4% до 0,3%.
Не бойтесь комбинировать методы. Установите входной инструментальный контроль сырья, промежуточный — по ключевым параметрам, финальный — с использованием методы контроля качества через независимое подразделение. Введите обязательную фотофиксацию результата: это помогает не только дисциплинировать персонал, но и быстро разбирать спорные вопросы. Прежде чем внедрить новый инструмент, проведите тренинг: бельевая простота работы с оборудованием увеличивает темп изготовления и снижает нагрузку на операторов.
Важно работать с поставщиками, а не только контролировать их. Открытый аудит, обмен лучшими практиками, совместные рабочие встречи зачастую выявляют слабые места не на входе, а на этапе заказа. Представьте, что вы на этапе закупки уже проверили сплав на соответствие, согласовали допуски, провели совместный тест. На практике в европейских компаниях такие меры снизили число рекламаций на 45% — это статистика, которую приводил журнал Manufacturing Today.
Автоматизация процесса не решит всех проблем, если контроль качества лишь галочка в документах. Обсудите с коллективом способы мотивации: от поощрений за креативные методы выявления брака до небольших премий за экономию на перепроверках. Иногда сотрудники предлагают решения, которые в разы эффективнее официальных регламентов.
Держите наготове план реагирования на дефект. Если нашли серию сомнительных деталей — быстро решите, что делать: возвращаем на доработку, отправляем на анализ, списываем или используем частично. Промедление затормаживает всю цепочку. На крупных предприятиях внедряют системы быстрых уведомлений и «горячие столы качества»: находка дефекта моментально попадает руководству и службе ОТК.
Не забывайте про обучение. Даже самый современный прибор не спасёт, если оператор не понимает, как его калибровать. Практика показала: чем чаще проводится обучение персонала, тем ниже «скрытый» процент брака — тот, что уходит сквозь сито стандартных проверок.
Одно новое решение не заменит системного подхода. Применяйте разные инструменты контроля, анализируйте статистику, поддерживайте связь с поставщиками и не жалейте времени на тренинги — вот простой и честный рецепт борьбы с производственным браком. Контроль качества — не дракон, которому нужны жертвы, а система, позволяющая быть уверенным, что твой продукт переживёт испытания временем, дорогой и… самым строгим клиентом.