Почему важно качество в машиностроении: разбор без прикрас
Все слышали: «Качество важнее количества». В машиностроении это — не просто красивый лозунг. От качества зависят деньги, жизнь людей, будущее бизнеса. Один бракованный болт может обойтись дороже, чем вся партия деталей вместе.
Знаете, почему в Европе и Японии машины служат дольше? Дело не в волшебстве, а в жестком подходе к качеству на каждом этапе. Там проверяют не только итоговый продукт, но и каждый шаг: от чертежей и сырья до упаковки готовой детали. И чем раньше выявляют ошибку, тем меньше убытков. Простой пример: если обнаружить микротрещину на заготовке на старте, исправление обойдется в пару рублей. Если пропустить — с нее сойдут сотни дефектных деталей, которые могут попасть на рынок.
- Качество — фундамент безопасности и репутации
- Типичные ошибки и чем они оборачиваются
- Лучшие практики контроля качества
- Роль сотрудников: почему от каждого зависит результат
- Советы и инструменты для повышения качества
Качество — фундамент безопасности и репутации
Вы когда-нибудь задумывались, почему в машиностроении заводы могут потратить тысячи часов на проверку одной детали? Это не перестраховка, а необходимость. Качество — это не только про срок службы техники. В первую очередь, оно — про безопасность.
Реальный пример: автоконцерн Toyota в 2010 году отозвал более 8 миллионов машин из-за дефекта в педали газа. Причём дефект находился даже не в электрике или моторе, а в маленькой пластиковой детали. Итог — сотни миллионов долларов убытков, а главное — подорванное доверие к бренду.
Почему такое возможно? Дело именно в мелочах. Один дефект может привести к аварии, порче продукции или даже человеческим жертвам. Вот чем опасно экономить на контроле качества в машиностроении:
- Рост аварий и брака, что порой может привести к травмам или смертям.
- Юридические риски — пострадавшие клиенты могут подать в суд.
- Потеря контрактов с крупными заказчиками. Никто не хочет работать с поставщиком, чья продукция ломается.
- Ремонт по гарантии настолько дорог, что часто легче отозвать всю партию.
- Репутационные потери. Ошибка одного цеха — удар по всей фирме на годы вперёд.
Есть интересная цифра: исследование в Германии показало, что каждый евро, вложенный в систему управления качеством, экономит 7–8 евро на возвратных издержках и ремонте. То есть не проверять — значит просто выбрасывать деньги на ветер.
А теперь представьте заводы, где такой подход игнорируют. Работники закрывают глаза на царапины, не тестируют изделия, ссылаясь на «и так сойдёт». Через месяц-два у фирмы уже нет покупателей, а после пары аварий с техникой — и лицензии на производство.
Задача каждого, кто работает в машиностроении, помнить: качество — это не табличка на стене, а вопрос выживания компании и безопасности миллионов людей.
Типичные ошибки и чем они оборачиваются
Промахи в машиностроении случаются чаще, чем кажется. Ошибки на производстве бывают не только из-за устаревших станков, но и из-за человеческого фактора, неправильной документации или банального невнимания. Вот какие факапы встречаются особенно часто:
- Использование некачественного металла или комплектующих — экономия на сырье часто приводит к отказам техники уже через год эксплуатации.
- Несоблюдение техпроцессов — если пресс или сварка работают «на глаз», никто не гарантирует прочность конечного изделия.
- Ошибка в чертежах или размерах — деталь не проходит контроль, и приходится переделывать целую партию.
- Слабый контроль качества на промежуточных этапах — если проверка только на выходе, легко не заметить скрытые дефекты.
Один пример на память: в 2021 году известный автопроизводитель отозвал больше 400 тысяч машин из-за мелкой ошибки в гайке крепления тормозного шланга. Сэкономили на копейках, а потеряли миллионы долларов и доверие клиентов.
Есть и статистика:
Тип ошибки | Обычная причина | Последствия |
---|---|---|
Брак сварки | Недостаточная температура, плохое сырье | Может привести к разрушению техники |
Неверный размер детали | Сбой станка, ошибка оператора | Остановка сборочной линии, затраты времени на переделку |
Поверхностные дефекты | Пыль, грязь, нет контроля | Отказ детали в работе, жалобы клиентов |
Как говорит эксперт Сергей Иванов, директор по управлению качеством одного из заводов:
«Любая производственная ошибка — это не только деньги и время. Это репутация и повторяемость проблем, если вовремя не разобраться с причинами».
По факту, даже единичная ошибка может вырасти в огромные потери. Особенно если она уйдёт дальше — в транспорт, стройку или медицину. Расчёт тут простой: чем раньше нашли проблему, тем дешевле и проще её исправить.
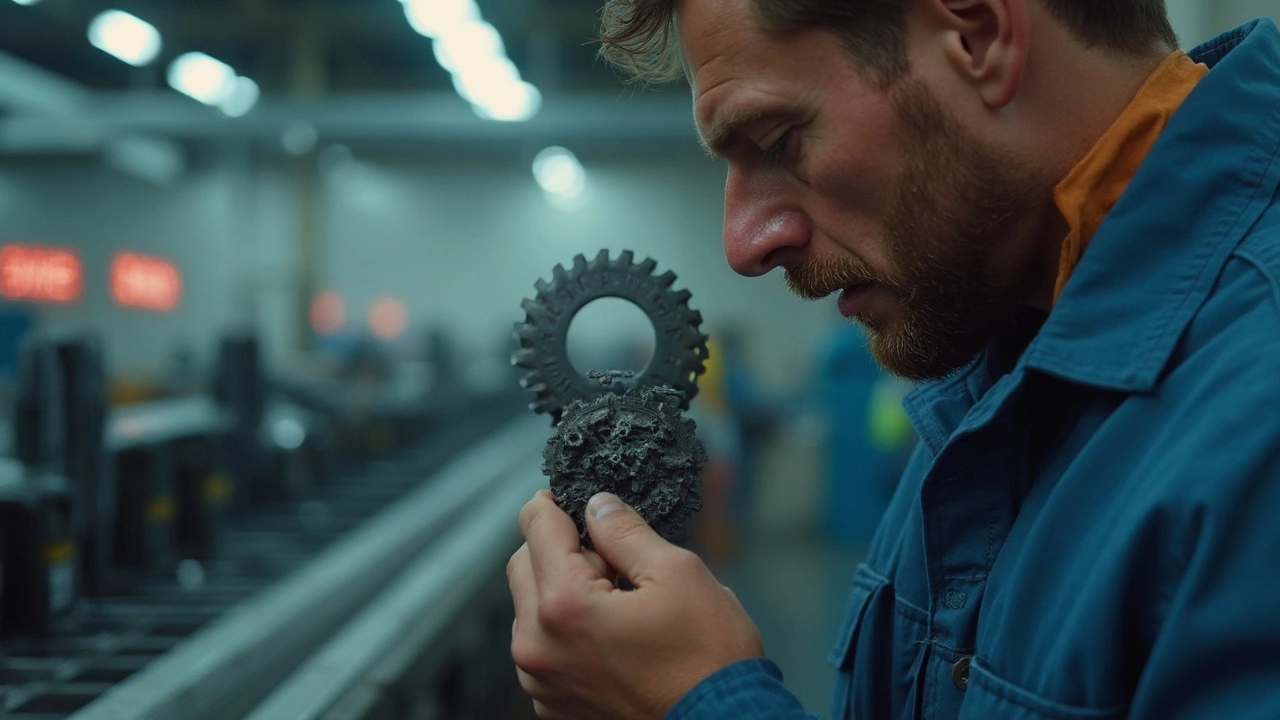
Лучшие практики контроля качества
В мире машиностроения слабый контроль оборачивается потерями и ненужными расходами. Здесь нельзя полагаться только на честное слово — нужен строгий подход. Одна из ключевых идей: вся система управления качеством строится на чётких процедурах. Если схема выстроена правильно, риск брака минимальный.
Во многих современных компаниях проверяют не только саму деталь, но и все процессы вокруг. Это называется многоуровневый контроль. Вот как это выглядит на практике:
- Входной контроль сырья — материалы проверяют до того, как они попадут в производство.
- Промежуточный контроль — после каждого этапа создают статистику по ошибкам и выявленным отклонениям.
- Итоговая проверка — перед отправкой детали клиенту ещё раз смотрят соответствие стандартам.
- Аудит производства — независимые специалисты периодически оценивают всю цепочку производства и подсказывают, где слабое место.
Не исключают автоматизацию: теперь датчики и умные камеры выявляют микроскопические дефекты, которые человек легко бы пропустил. Например, на крупных заводах внедряют компьютерные системы контроля размеров, и даже небольшое отклонение сразу фиксируется.
Есть интересные цифры. В 2023 году одно из питерских предприятий, внедрив автоматическую систему слежения за качеством, снизило процент брака с 2,8% до 1,2% всего за полгода. Такой результат достигается, когда контроль не превращается в формальность, а становится реальной повседневной практикой.
Этап контроля | Обнаружено брака (%) |
---|---|
Входной (сырье) | 0,6 |
Промежуточный | 0,4 |
Итоговая проверка | 0,2 |
Чтобы система работала, нужно, чтобы все вовлечённые были в одной лодке. Это не только отдел контроля качества, но и рабочие на станках, технологи, логисты. Важно постоянно обучать персонал, объяснять, зачем всё это нужно. Недостаточно просто проверить деталь на выходе — важно понимать, где сбой мог произойти на пути к готовому продукту, и как его предотвратить в будущем.
Роль сотрудников: почему от каждого зависит результат
В машиностроении каждый человек на линии, в отделе контроля, в офисе — это часть большой цепи. И если кто-то один халатно отнесется к своей задачи, пострадает общий результат. Тут не работают схемы «моя хата с краю». Даже уборщица влияет на качество, потому что лишний мусор на станке — это риск для изделия и станка.
В России ещё недавно бытовало мнение: «Пусть брак потом найдут в ОТК». Но статистика говорит обратное. На одном из крупных автозаводов выявили, что если проблему видит только служба качества на финальном этапе, расходы на устранение дефекта могут вырасти в 5-7 раз. А если ошибку заметил оператор у себя на рабочем месте, издержки минимальны.
Вот, кто особенно влияет на управление качеством на производстве:
- Операторы станков — первыми видят сбои и отклонения, могут остановить процесс до проблемы.
- Наладчики и механики — отвечают за техническое состояние оборудования, чтобы оно работало без сбоев.
- Кладовщики и снабженцы — обязаны следить, чтобы материалы были качественными и срок годности не истек.
- Инженеры и технологи — проектируют процессы так, чтобы уменьшить вероятность брака.
- Контролеры ОТК — последний рубеж, но не единственный.
Кстати, большинство известных случаев массового брака начинались с безобидной «мелочи»: недоглядел деталь в упаковке, поленился внести запись о неполадке, решил «прокатит и так». На практике одна ошибка сотрудника способна умножиться десятками недочетов.
Работающие советы, которые реально помогают:
- Внедрять простую обратную связь — чтобы любой мог сообщить о проблеме без страха.
- Проводить короткие брифинги перед сменой по особенностям задач и контрольных точках.
- Ротация — иногда смена участка помогает быстрее замечать ошибки.
Пункт контроля | Когда выявлен дефект | Средние издержки на устранение |
---|---|---|
На рабочем месте оператора | Сразу после изготовления | ≈ 1 000 руб. |
На линии ОТК | До упаковки | ≈ 5 000 руб. |
У клиента | После продажи | 30 000 руб. и выше + ущерб репутации |
Общий смысл: каждый ответственен. Качество — это не отдел, а стиль работы всего коллектива. Когда коллеги видят свою роль и понимают последствия, количество брака падает почти вдвое. Тут важна честность, внимание к деталям и уважение к своей работе.
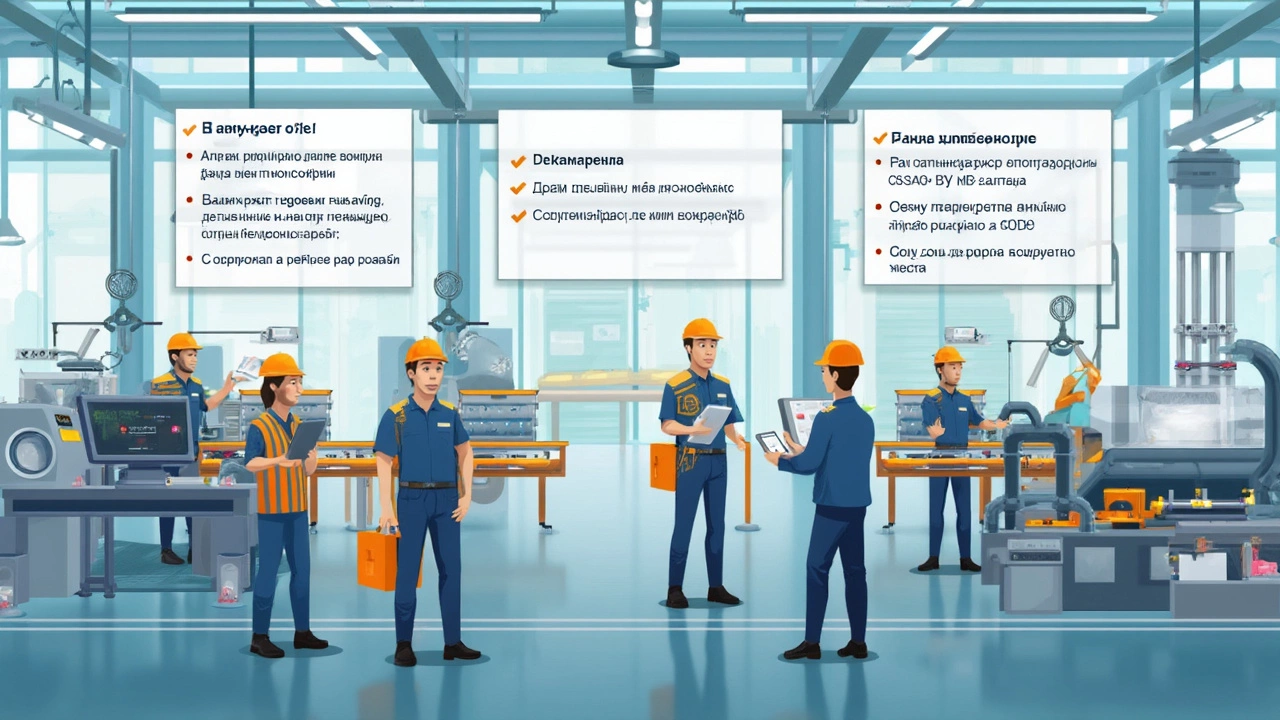
Советы и инструменты для повышения качества
Когда речь идёт о качестве в машиностроении, мелочей не бывает. Хочешь меньше брака — начинай с дисциплины и инструментов, которые реально работают. Вот несколько практических советов:
- Внедряй контроль на каждом этапе. Не экономь время на промежуточных проверках. Чем раньше найдёшь ошибку, тем ниже затраты на исправление. Проверяй сырьё прямо на входе, контролируй операции на линии, инспектируй даже упаковку.
- Используй чек-листы для каждого процесса. Простой бумажный или электронный чек-лист плющит человеческий фактор. Рабочий отмечает: сделал, глянул, проверил. За день реально отловить десятки мелких косяков.
- Автоматизируй процессы, где это возможно. Программы и датчики ошибаются реже, чем человек. Например, система контроля размеров деталей сразу покажет, если идут отклонения по допускам — не надо ждать конца смены.
- Обучи персонал стандартам качества. Даже оператор на станке должен понимать, почему его работа влияет на чужую безопасность. Проводить короткие обучения раз в месяц? Просто, недорого и прямо влияет на количество брака.
- Проводить аудит поставщиков. Иногда проблема не в своих руках, а в закупках. Регулярно проверяй тех, кто поставляет материалы и комплектующие.
Есть конкретные инструменты, которые уже показали результат:
- Система 5S. Наведи порядок на рабочем месте. Это не просто уборка, а система для предотвращения потерь и брака.
- FMEA (анализ видов и последствий отказов). Запланируй возможные ошибки заранее, оцени риск и внеси исправления в процесс.
- SPC (статистический контроль процессов). Используй графики и данные для отслеживания стабильности производства. Чем стабильнее процесс — тем выше качество деталей.
Интересный факт: на одном из заводов в Подмосковье после внедрения электронных систем отслеживания ошибок уровень брака снизился с 4,3% до 1,1% за полгода. Просто потому, что любой косяк сразу выплывал наружу, и его устраняли до того, как он стал проблемой для клиента.
Инструмент | Результат применения |
---|---|
Электронные чек-листы | Сокращение времени на проверку на 15% |
Система 5S | Снижение потерь и простоев на 25% |
SPC | Раннее выявление нестабильности процесса |
Всё это не про дорогие инновации. Большинство приёмов можно внедрить за пару недель, а результат не заставит себя ждать. Главное — не закрывать глаза на косяки и делать ставку на управление качеством.