Проблемы машиностроительного комплекса на современном этапе: что важно знать
Машиностроение когда-то считалось флагманом российской экономики. Сегодня всё чаще всплывают вопросы: почему новые станки закупают за границей? Почему молодёжь не спешит работать на заводах? Ответ прост — у отрасли накопился целый ряд проблем, которые мешают двигаться вперёд. И дело не только в сложной технике или дефиците денег.
Если вы работаете на заводе или просто интересуетесь машиностроением, вы наверняка сталкивались с бытовыми трудностями: не хватает инженеров, приходится искать детали под заказ за границей, оборудование устаревает быстрее, чем завод может себе позволить модернизацию. Всё это — не отдельные случаи, а настоящая система, с которой сталкиваются большинство предприятий по стране.
Хочется понять, что именно мешает развитию. Ведь за решениями часто скрыты вполне приземлённые вопросы: сколько ждать запчасти из Европы, почему программное обеспечение постоянно «глючит», и как получить молодого «технаря», если все хотят в IT или маркетинг. Эти моменты волнуют не только директоров, но и простых рабочих.
- Барьеры для развития: что тормозит отрасль
- Кадровый голод: почему не хватает специалистов
- Технологическая отсталость и как с ней бороться
- Импортозамещение: реальность или миф
- Инвестиции и поддержка государства
- Где искать выход: практические шаги
Барьеры для развития: что тормозит отрасль
Машиностроительный комплекс сталкивается с проблемами, которые тянутся годами. Первый, кто это замечает — обычные рабочие: они каждый день видят, как не хватает оборудования, а запчасти приходится ждать месяцами. Часто звучит жалоба: станки, купленные в 90-х, морально устарели, и давно пора обновить парк техники.
Самая горячая тема последних лет — это зависимость от импорта ключевых компонентов. Например, почти 45% станков, которые сегодня работают на крупных заводах, произведены за границей (данные Минпромторга на 2024 год). Россия пока не добилась самостоятельности в этом направлении.
«Без реальных инвестиций в обновление оборудования мы не сможем конкурировать даже на внутреннем рынке», — отмечает Сергей Михайлов, глава ассоциации производителей машиностроения.
Но и дело не только в технике. Много спотыкаются о бюрократию: оформление документов, длинные согласования, непонятные сертификационные требования. Это задерживает запуск новых проектов и обновление производства.
- Дорогое кредитование. Процентные ставки для машиностроителей выше, чем в развитых странах — сложно брать новые кредиты на расширение производства.
- Износ зданий и инфраструктуры. По оценкам Росстата, в среднем 55% промышленных зданий нуждаются в ремонте или полной реконструкции.
- Рост цен на сырье (сталь, цветные металлы) напрямую бьет по себестоимости готовой продукции.
Вот простая таблица — видно, с какими барьерами чаще всего сталкиваются предприятия:
Проблема | Доля предприятий, столкнувшихся (%) |
---|---|
Изношенное оборудование | 63 |
Импортозависимость | 47 |
Бюрократия | 39 |
Недоступность кредитов | 35 |
Многие заводы вынужденно сокращают объёмы, потому что не могут позволить себе закупку даже простейших комплектующих. Это тормозит не только машиностроение, но и всю промышленность.
Если свести всё к короткому выводу — главный тормоз для машиностроения сейчас это старое оборудование, импортозависимость и бумажная волокита. Без борьбы с этими барьерами о технологическом рывке можно даже не мечтать.
Кадровый голод: почему не хватает специалистов
Вот где самое уязвимое место в машиностроении — нехватка людей с нужными навыками. На заводах не только не хватает опытных токарей и инженеров, но и просто желающих освоить эти рабочие профессии. Абитуриенты выбирают ИТ, экономику, сервис — туда, где скользко на пальцах, а не грязно в цеху. К тому же, вузы по-прежнему учат по устаревшим учебникам, где современные станки упоминаются вскользь, а цифровые технологии вообще остаются в тени.
Самое смешное: зарплаты инженеров в машиностроении часто ниже, чем даже у начинающих айтишников. В итоге, у предприятий выбор невелик — или нанимать работников старшего возраста (часто уже пенсионеров), или тратить большие деньги на обучение своих стажёров с нуля.
Посмотрите на эти цифры. Согласно данным Минобрнауки РФ за 2024 год, выпускников, которые идут работать по специальности «Машиностроение», меньше чем 30% от всех закончивших профильные техникумы и вузы. Эксперты Росстата подтверждают: средний возраст инженера по оборудованию уже приближается к 50 годам.
Показатель | 2022 | 2024 |
---|---|---|
Доля молодых специалистов на заводах, % | 14 | 11 |
Средний возраст инженера, лет | 46 | 49 |
Сколько выпускников работает по профессии, % | 36 | 28 |
Причин тут несколько:
- Образование не даёт практических знаний по современным технологиям.
- В отрасли часто низкий заработок и устаревшие социальные гарантии.
- Имидж машиностроителя давно потерял привлекательность для молодежи.
- Нет системы наставничества, а на стажировки студентов смотрят как на дополнительную обузу.
Решить проблему поможет только комплексный подход. Заводы могут сотрудничать с вузами, чтобы делиться реальными задачами, а государство — поддерживать молодых инженеров грантами и бонусам за работу в машиностроении. Так хотя бы появится шанс не потерять отрасль совсем.
Технологическая отсталость и как с ней бороться
Почему российское машиностроение часто называют отсталым? Ответ прямо на поверхности: большинство заводов до сих пор работают на оборудовании, которому больше двадцати лет. Для сравнения: в Южной Корее и Японии средний возраст станков — 5-7 лет. Это влияет на всё: качество продукции, скорость производства, даже безопасность рабочих.
Вот факты. Доля современных станков с программным управлением (ЧПУ) в российских компаниях не превышает 25%. Для Европы этот показатель — больше 60%. Ниже таблица, чтобы было нагляднее:
Страна | Доля станков с ЧПУ, % |
---|---|
Россия | 25 |
Германия | 65 |
Китай | 50 |
Почему так вышло? Во-первых, закупка нового оборудования требует больших вложений, а кредиты для заводов зачастую недоступны или слишком дорогие. Во-вторых, многие техпроцессы до сих пор ведут вручную — просто потому, что не хватает АйТи-специалистов для автоматизации. В-третьих, отсутствие доступа к оригинальному ПО после ухода западных компаний — реальная головная боль для многих предприятий.
С этим точно нужно что-то делать. Вот реальные шаги, которые уже сейчас применяют некоторые предприятия и которые может взять на заметку любой производственный руководитель:
- Переход на отечественное ПО для станков. Несовершенно? Да, но его можно дорабатывать под свои задачи.
- Внедрение гибких производственных линий. Даже обычные роботизированные манипуляторы могут «оживить» цех.
- Совместные проекты с вузами — для поиска инженерных решений и кадровой поддержки. Это реально работает: на заводах, сотрудничающих с профильными университетами, внедрение новых технологий идёт быстрее на 20%.
Можно долго ждать чуда, а можно прямо сейчас начать с мелочей — например, оцифровать документацию, автоматизировать учёт деталей, наладить обмен опытом с другими предприятиями через отраслевые ассоциации. Все эти решения не требуют астрономических вложений и реально помогают снизить технологический разрыв.
Кому выгодно развивать машиностроение? Всем, кто хочет оставаться конкурентоспособным. Деградация технологий — прямой путь к потере заказчиков, сокращению рабочих мест и зависимости от внешних рынков. А выбраться из этого круга можно только через постоянное внедрение новых идей и отказ от подхода «работаем по-старинке».
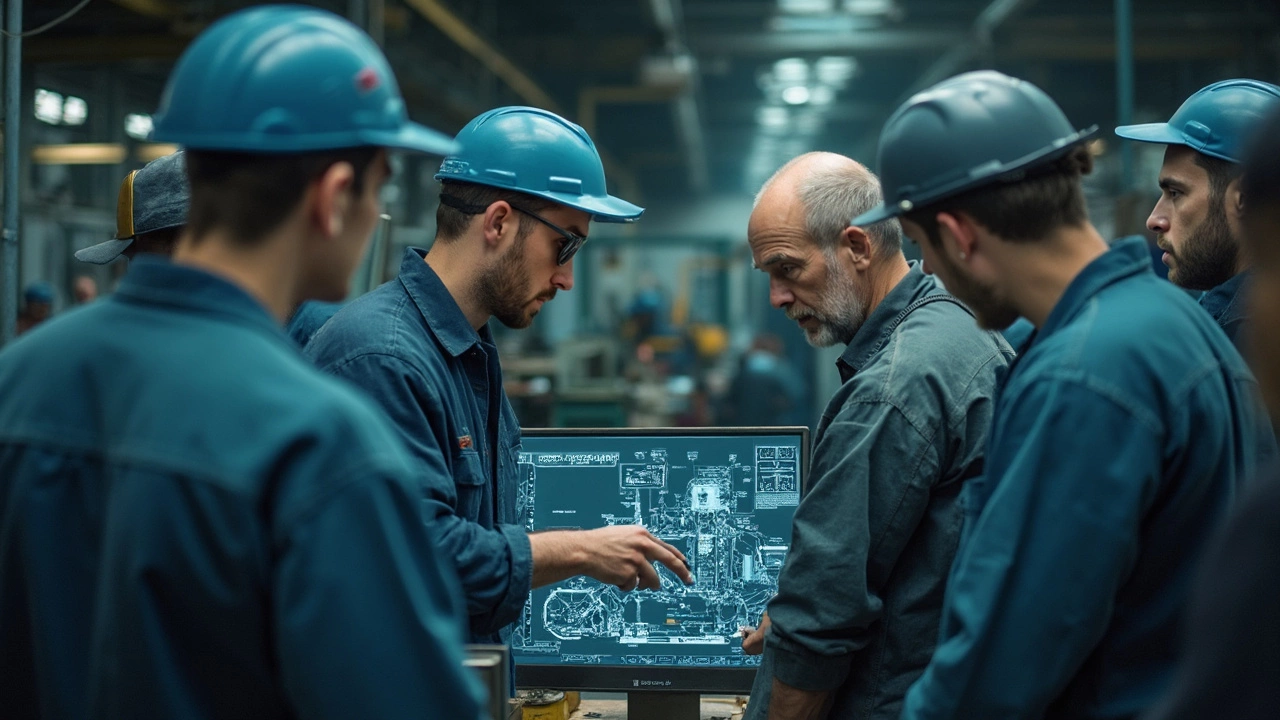
Импортозамещение: реальность или миф
Импортозамещение обсуждают на каждом промышленном форуме и круглых столах. Кажется, уже лет десять говорят: вот-вот, скоро начнём производить всё своё, не хуже, чем в Европе или Азии. Но если спуститься с высоких слов на производство — всё не так гладко.
Реальная жизнь часто расходится с планами на бумаге. Из-за санкций и скачков курса рубля закупать комплектующие стало дороже и дольше, а не всегда есть чем их заменить. Например, российские станки пока не могут полноценно конкурировать с японскими и немецкими по точности и надежности. Почти 65% ключевого оборудования, по оценкам Ассоциации станкостроителей России, в 2024 году всё еще импортное.
Категория | Доля импортных решений в 2024 г., % |
---|---|
Станки с ЧПУ | 70 |
Промышленные роботы | 80 |
Электроника для автоматизации | 75 |
Программное обеспечение | 90 |
Локализация деталей идёт, но слишком медленно. Часто под импортозамещением скрывается просто сборка из иностранных компонентов на российском предприятии. Некоторые заводы даже вынуждены разбирать старые европейские станки ради редких запчастей.
Но есть и позитивные моменты. В 2023 году доля российских комплектующих в машиностроении выросла на 12%. Центры разработки в Санкт-Петербурге и Екатеринбурге начали выпускать альтернативы западному ПО для проектирования, пусть пока и с ограниченным функционалом. Появились новые игроки, кто делает хорошие гидравлические системы и детали для грузовых автомобилей.
- Проверяйте, где действительно идёт производство, а где ограничиваются наклейкой российского логотипа.
- Обратите внимание на малый и средний бизнес: они часто двигают импортозамещение быстрее, чем гиганты.
- Не стесняйтесь тестировать новые отечественные решения, но сравнивайте их напрямую с импортными по качеству и цене.
Пока импортозамещение — больше задача, чем победа. Но отрасль двигается, пусть и медленно. Здесь важно не гнаться за красивыми отчетами, а честно смотреть на результат и делиться опытом. Тема машиностроение была и остаётся зоной риска, но и возможностью для роста.
Инвестиции и поддержка государства
Когда говорят о развитии машиностроения, все сразу вспоминают про субсидии и гранты. Без господдержки многим заводам и не выжить: новые станки, качественное сырье, обучение кадров — всё это требует вложений, которых просто нет у типичного производителя.
Факт: по оценкам Министерства промышленности и торговли РФ, общий объём прямых господдержки на машиностроение в 2024 году превысил 115 миллиардов рублей. Доля вложений из федерального бюджета составила более 60% от общего объёма инвестиций в отрасль. Такой уровень помощи редко встречается в других секторах, но деньги распределяются неравномерно. Крупные предприятия получают основную часть, а средний и малый бизнес часто остается за бортом.
Нередко выделение средств проходит по сложной и долгой бюрократической цепочке. Вот какие виды поддержки реально доступны сейчас:
- Субсидии на закупку и модернизацию оборудования (через Минпромторг)
- Льготные кредиты для промышленных предприятий
- Федеральные программы по переобучению и подготовке персонала
- Гранты на внедрение новых технологий
- Гарантийные фонды для инвестиционных проектов
Но если сравнить уровень инвестиций с Китаем или Германией, Россия пока проигрывает в абсолютных цифрах. Это сказывается на техническом отставании и конкурентоспособности. Обратим внимание на основные показатели за последние 3 года:
Год | Инвестиции (млрд руб.) | Часть господдержки (%) |
---|---|---|
2022 | 89 | 57 |
2023 | 102 | 59 |
2024 | 115 | 62 |
Труднее всего получить крупные инвестиции небольшим заводам — у них нет ресурсов на бумажную волокиту. Совет: отслеживайте региональные программы поддержки и работайте с местными центрами «Мой бизнес» — они реально помогают найти правильную дорогу к финансированию.
Если бы поддержка распределялась равномернее, машиностроение могло бы получить куда больший толчок. Тут выигрывают те, кто не ждёт «манны» сверху, а сам ищет гранты, инвесторов и не боится стучаться во все двери. Рынок меняется быстро, и тут спасают только скорость и умение находить решения здесь и сейчас.
Где искать выход: практические шаги
Махать рукой и говорить «все сложно» — самый легкий путь. Но в машиностроении хватает примеров, когда реальные действия меняли ситуацию на местах. Вот что может реально помочь отрасли не скатиться в застой.
- Ставка на переобучение и стажировки: Уже работает модель обучения на заводе, где студенты приходят не просто на экскурсию, а месяцами работают на реальном производстве. В 2024 году такие стажировки прошли 14 тысяч студентов по стране.
- Льготы для внедрения новых технологий: В ряде регионов предприятия получают налоговые послабления при закупке цифрового оборудования. Например, по данным Минпромторга, это позволило в прошлом году обновить парк станков на 11% быстрее, чем до льгот.
- Совместные кластеры с вузами: Пример — технопарк в Самаре, где университет и завод объединяют лаборатории и разрабатывают прототипы для промышленности прямо на месте. Выпускники переходят в штат — минус одна проблема с кадрами.
- Гибкое импортозамещение: Смотреть не только на полную замену комплектующих, а выстраивать сеть партнерств с малым бизнесом, который может производить специфические детали.
Без цифр и реальных изменений не получится ничего, поэтому вот таблица по тем мерам, которые чаще всего дают результат:
Шаг | Результат/Данные 2024 |
---|---|
Долгосрочные стажировки студентов | Рост трудоустройства выпускников на заводы на 22% |
Инвестиции в цифровизацию | Снижение производственных простоев на 9% |
Налоговые льготы для предприятий | Увеличение закупки нового оборудования на 11% |
Сотрудничество с вузами | Число внедренных разработок выросло на 15% |
Не стоит ждать чуда от одной-двух мер. Только комбинация переобучения, вложений в технологии и тесного сотрудничества с вузами даёт долгосрочный эффект. Если в регионе до этого руки не дошли — есть смысл посмотреть, что уже работает у соседей.