Три основных типа контроля качества в машиностроении
Контроль качества на предприятиях машиностроительной отрасли чаще всего включает несколько этапов, каждый из которых несёт свою особую нагрузку. В современных условиях качества и надежности изделий придается первостепенное значение, что делает этот процесс не столько обязательным, сколько жизненно важным для успеха любящей себя компании.
Куда важно смотреть: от самого начала производства — начиная с входного контроля материалов, через важный промежуточный контроль, и заканчивая итоговой проверкой готовой продукции. Рассмотрим подробно каждый тип, чтобы понять, как они помогают поддерживать высокий стандарт качества и не упустить никакой важной детали.
- Входной контроль материалов
- Промежуточный контроль процессов
- Выходной контроль продукции
- Советы по улучшению контроля качества
Входной контроль материалов
Входной контроль материалов является первым и ключевым шагом в обеспечении высокого уровня качества продукции в машиностроении. Задача этого этапа – убедиться, что все материалы, поступающие в производство, соответствуют установленным стандартам качества и техническим условиям. Именно на этом этапе закладываются основы для отсутствия брака в конечной продукции, поэтому важность входного контроля трудно переоценить. Недостаточный контроль на данном этапе может привести к дефектам в готовых изделиях, увеличению производственных затрат и, как следствие, к финансовым потерям предприятия. Это особенно актуально в случае работы с дорогими и редкими материалами, где ошибка может стоить крайне дорого.
Процедура входного контроля включает несколько этапов, начиная с документальной проверки, где инспектируются сертификаты и технические паспорта материалов. Эти документы дают общее представление о характеристиках поступивших товаров и их соответствии нормативным требованиям. Проведение лабораторных анализов и испытаний образцов - следующий критический шаг. С помощью специального оборудования материалы проверяются на физические и химические свойства, такие как прочность, жесткость, стойкость к коррозии и другие важные параметры. Проведённые испытания позволяют адаптировать процесс производства под специфические свойства материалов, что повышает управление качеством и выработку изделия при соблюдении высоких стандартов.
Интересный факт, если обратиться к статистике, можно отметить, что по данным Международной организации по стандартизации (ISO), более 60% дефектов выявляется именно на этапе входного контроля. Это доказывает необходимость тщательной проверки всех характеристик продукции, чтобы остальные этапы производства не приводили к значительным затратам на исправление таких дефектов впоследствии.
"Контроль качества начинается с качественных материалов. Если исходное сырьё не соответствует ожиданиям, качество продукции будет страдать, как бы вы ни стремились его улучшить." - Джэми Форд, эксперт в области управления производством.
Стратегии входного контроля также включают использование методов статистического анализа для прогнозирования потенциальных проблем. Это помогает не только избегать ошибок, но и оптимизировать процесс и повысить качество машиностроительной продукции без ущерба для времени производства. Внедрение технологий машинного обучения и автоматизации процесса контроля способствует скорейшему и более точному обнаружению несоответствий в характеристиках материалов. Таким образом, входной контроль материалов служит как первый щит против пагубных последствий низкого качества, помогая закладывать крепкий фундамент для безопасной и надежной продукции в машиностроении.
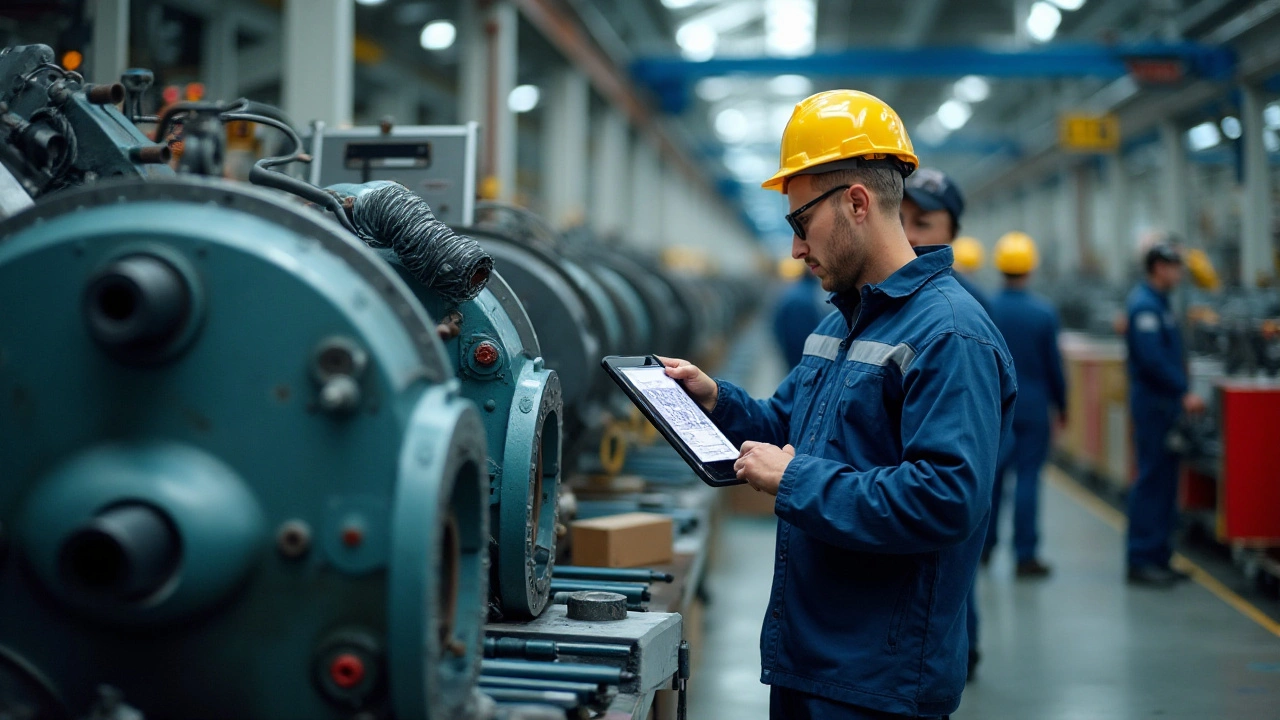
Промежуточный контроль процессов
Промежуточный контроль процессов играет ключевую роль в управлении качеством на стадии производства в машиностроении. Этот этап позволяет выявить дефекты и несоответствия на ранних стадиях, когда их исправление не требует значительных затрат и усилий. Основная цель - предотвратить попадание неисправных компонентов в последующие стадии сборки, тем самым обеспечивая высокую надежность и качественность конечной продукции.
Процесс промежуточного контроля складывается из нескольких аспектов: проверка работоспособности отдельных узлов и элементов, анализ производственных параметров, контроль соблюдения технологических режимов. Обычно на этом этапе используется как визуальный, так и инструментальный методы контроля. Визуальный подход позволяет быстро обнаружить очевидные отклонения или дефекты, в то время как инструменты, такие как ультразвук и инфракрасный анализ, служат для более детального анализа неполадок, скрытых от человеческого глаза.
Интересно, что внедрение новейших технологий значительно упрощает задачи промежуточного контроля. Системы машинного зрения и искусственного интеллекта способны не только выявлять дефекты быстрее, но и анализировать их, помогая предсказать возможные сбои. Например, в своем исследовании компания GE заявила:
"Искусственный интеллект и машинное обучение в процессе контроля позволяют нам увеличить эффективность обнаружения дефектов на 30%", - отмечает представитель компании.
Для повышения эффективности промежуточного контроля рекомендуется внедрение системы отслеживания качества процессов (SPC - Statistical Process Control). Эта методика предполагает постоянный сбор данных о производственном процессе и их анализ с использованием статистических методов. В результате можно не только оперативно реагировать на отклонения, но и прогнозировать их появление, предотвращая возможные срывы производственного цикла.
При рассмотрении промежуточного контроля в контексте управления качеством, нельзя обойти стороной важность обучения персонала. Компетентные и квалифицированные работники могут не только эффективно использовать передовые техники и технологии, но и адаптировать их под специфические потребности производства, что в конечном итоге приводит к улучшению всей системы контроля качества. Это один из факторов, влияющих на общий уровень надежности и эффективности всей производственной линии.
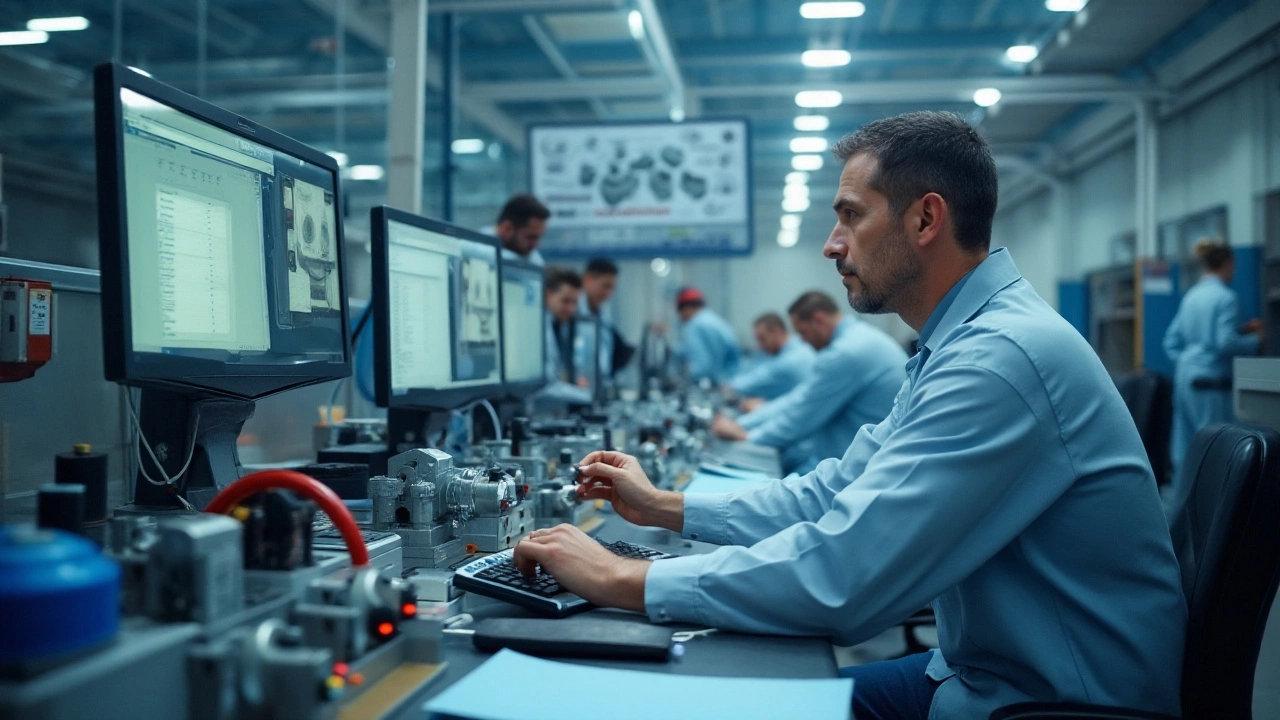
Выходной контроль продукции
Выходной контроль продукции – заключительный этап контроля качества, который играет решающую роль в системе обеспечения надежности и безопасности машин и оборудования. Этот этап включает в себя широкий спектр проверок и тестов, направленных на гарантию того, что конечный продукт соответствует установленным стандартам и спецификациям. Выходной контроль особенно важен в условиях жесткой конкуренции на рынке машиностроительной продукции, где каждая деталь может определять успех или неудачу.
На этапе выходного контроля проводятся всесторонние испытания готовой продукции, включая функциональные тесты, тестирование на устойчивость к различным нагрузкам и условиям эксплуатации, а также проверка на соответствие геометрическим параметрам и точностям сборки. Специалисты сталкиваются с задачами выявления скрытых дефектов, которые могли возникнуть в процессе производства, что делает этот этап особенно трудоемким. Исследования показывают, что качественный выходной контроль может уменьшить вероятность отказов изделия на 30%.
Василий Иванов, инженер с многолетним стажем, отмечает: "Качественный выходной контроль – это не только вопрос качества продукции. Это уважение к клиенту, их безопасности, и, в конечном счете, укрепление репутации самого производителя."
Одним из наиболее эффективных методов является применение автоматизированных систем для проверки качества готовой продукции. Они позволяют снизить влияние человеческого фактора и повысить точность измерений. По данным исследований, на заводах, применяющих автоматизацию, количество дефектов сокращается в 4 раза. Ключевая важность этого процесса в том, что он позволяет не только выявить брак, но и понять причины его возникновения, что способствует дальнейшему улучшению процессов управления качеством.
Внедрение строгих стандартов на этапе выходного контроля также помогает минимизировать обратные поставки и связанные с этим расходы. Это позитивно сказывается на общей эффективности производства, снижает себестоимость продукции и увеличивает прибыль компании в долгосрочной перспективе. Статистика утверждает, что компании, которые уделяют внимание данному аспекту, добиваются более стабильного роста на рынке.
Практические советы по улучшению выходного контроля
- Регулярная калибровка измерительных инструментов для поддержания их точности и надежности.
- Создание базы данных по результатам всех тестов и проверок для последующего анализа и улучшения оборудования.
- Постоянное обучение и повышение квалификации сотрудников отдела контроля качества.
Настоящая забота о выходном контроле продукции подтверждает обязательства компании перед заказчиками и конечными пользователями. Понимание важных аспектов этого процесса позволяет снизить риски возникновения остаточных дефектов и поддерживает высокую конкурентоспособность предприятий в сфере машиностроения.
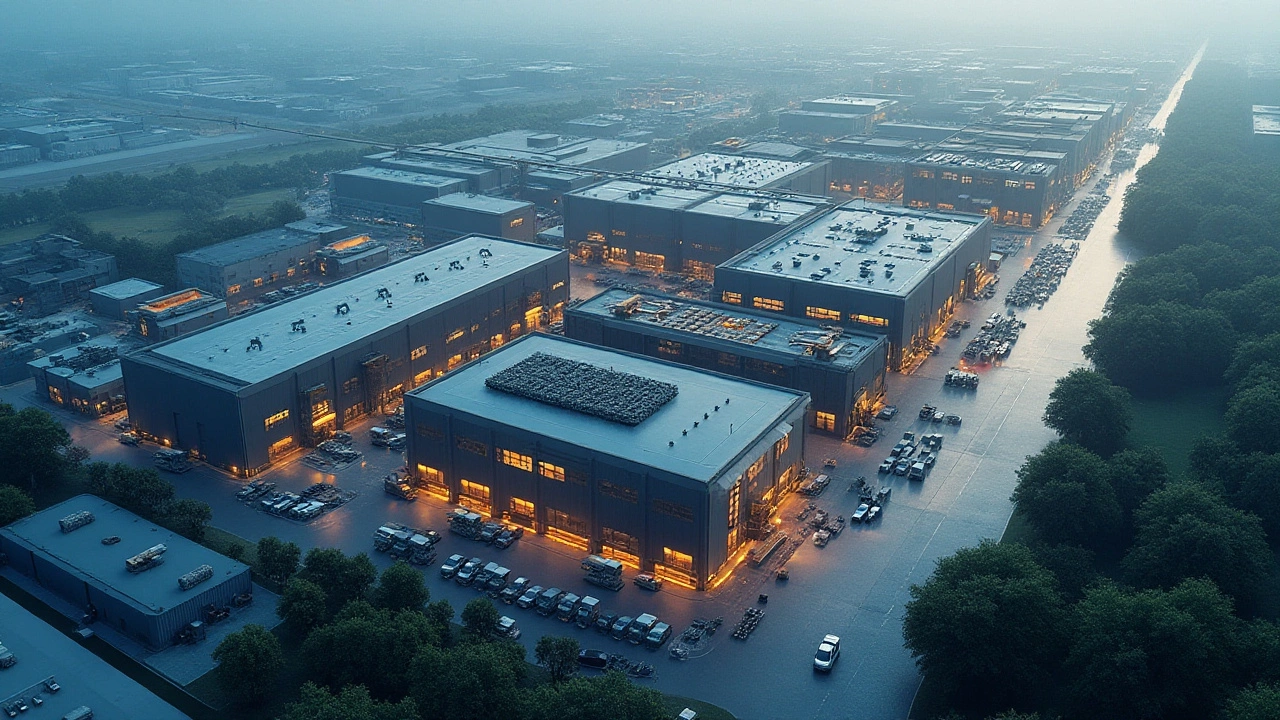
Советы по улучшению контроля качества
В сфере управления качеством в машиностроении крайне важно внедрять эффективные методы и техники, которые помогут повысить надежность и стандарты продукции. Один из ключевых советов — это создание специализированной команды по контролю качества. Такие команды должны состоять из экспертов, которые понимают все аспекты производства, технические спецификации и потенциальные узкие места в процессе. Эти группы могут эффективно разрабатывать стратегии и внедрять политики, направленные на устранение дефектов ещё до их появления, что в конечном итоге приведет к повышению качества продукции.
Также стоит обратить внимание на внедрение продвинутых технологий, таких как автоматизированные системы контроля. Эти системы позволяют не только ускорить процесс проверки, но и сделать его более точным и последовательным. Чтобы оценить, как эффективна технология, нужно адаптировать её под конкретные нужды предприятия, учитывая масштаб производства и тип используемых материалов. Важно помнить, что внедрение технологий должно быть плавным и сопровождаться обучением сотрудников, чтобы они могли максимально эффективно использовать новые инструменты.
"Качество - это вклад в будущее, и оно начинается с осознанного планирования на каждом этапе производства," - комментирует Даглас Хемингуэй, эксперт в области контроля качества.
Кроме того, для улучшения качества в машиностроительных процессах рекомендуется использование метода анализа корневых причин. Этот подход позволит выявить повторяющиеся проблемы и, что более важно, понять их причину. Проводя такие исследования, можно устранить не только текущие недостатки, но и создать план воспроизводства успешных решений в будущем. При анализе корневых причин можно использовать методы, такие как диаграмма «рыбья кость» и метод «пять почему». Контроль, построенный на осознании проблем, развивает в компании культуру постоянного улучшения.
Интеграция обратной связи
Ещё одним важным аспектом является интеграция обратной связи от клиентов. Производители должны активно искать отзывы пользователей и учитывать их при разработке новых продуктов. Например, создание условий, при которых производственные бренды могут эффективно собирать и анализировать отзывы клиентов о продукте, значительно поможет в улучшении его качества. Это не только укрепляет доверие клиентов, но и способствует созданию более конкурентоспособной продукции. Важно, чтобы такие отзывы становились частью процесса принятия решений на всех уровнях организации, начиная с отдела разработки продукции и заканчивая производственными мощностями.
Ключ к успеху — это наладка каналов связи между отделами контроля качества и другими подсистемами компании. Только таким образом можно добиться того, чтобы каждый шаг в производственном процессе учитывал текущие требования к качеству. Компании, которым удается поднять уровень взаимопонимания и поддержки между командами, более успешно справляются с вызовами современного рынка.